Zinc’s Bullish Narrative – Part 2 – A Look at Demand
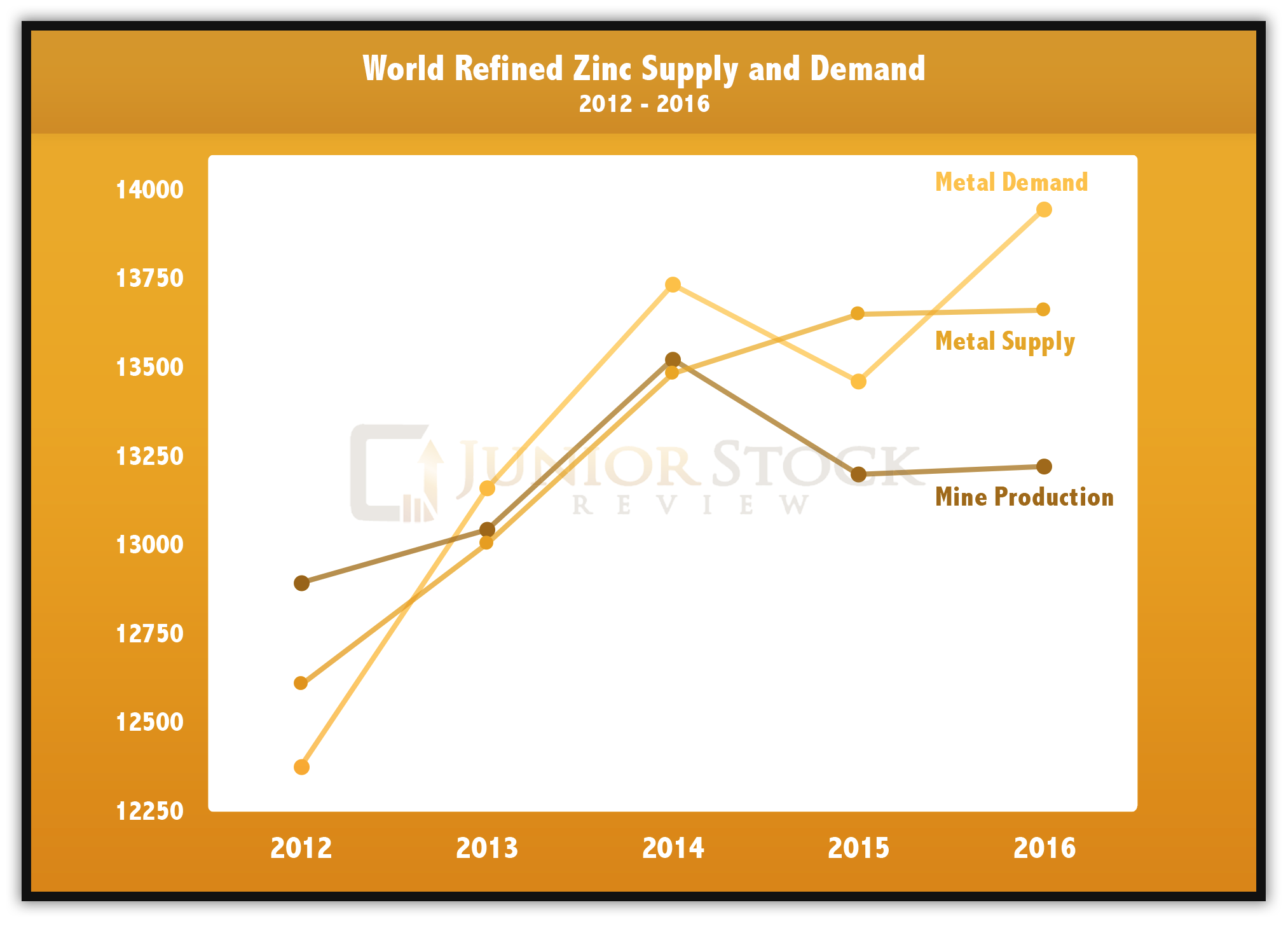
In Part 1 of this series on Zinc’s Bullish Narrative, I covered the supply side of the zinc market. Here, I’ll take a look at world zinc demand. Demand for zinc concentrate begins with the smelters and is where I will start.
Smelting
Smelting is integral to the zinc supply chain because, generally speaking, the end use manufacturers can’t use the zinc concentrate that’s created by the miners.
NOTE: Check out this video on zinc smelting
There are two methods for smelting the zinc concentrate:
- Pyrometallurgical
- Hydrometallurgical (Electrolytical)
Before the concentrate can enter one of these two smelting methods, it must be roasted or sintered. Roasting is used to remove the sulphur from the concentrate, which can represent anywhere from 25 to 30% of the concentrate. The concentrate temperature is brought up to 900 degrees Celsius and the zinc sulfide converts into zinc oxide. The sulfur then combines with oxygen and forms sulfur dioxide. Once the sulfur is removed, the concentrate can now be processed using either the pyrometallurgical process or the hydrometallurgical process to produce the near pure zinc.
NOTE – There are 3 types of roasters: Multiple hearth, suspension and fluidized bed.
Hydrometallurgical Process
90% of zinc is produced via the hydrometallurgical process. Here are the steps used in the process:
- Leaching – sulfuric acid is used to dissolve the zinc oxide, while leaving most, but not all of the other metals un-dissolved.
- Purification – the cementation process is used to purify the zinc further, with the addition of zinc dust, any of the remaining metals can be precipitated out.
- Electrolysis – an electrical current is sent between lead alloy anodes and aluminum cathodes, causing the zinc to come out of solution and deposit onto the cathode.
- Casting – the close to pure zinc is then removed from the cathode, dried, melted and finally casted into ingots. Zinc ingots typically range in purity from high grade 99.95% to special high grade 99.99%.
Pyrometallurgical Process
Due to the energy intensive nature of this process, only a few places in the world use the pyrometallurgical process. Zinc is refined in this process within an Imperial Smelting furnace. Because this process is rarely used I won’t go into any more detail.
Smelting Capacity
Source: International Lead and Zinc Study Group
As with zinc mine production, almost 50% of available smelting capacity is found in China. China is the hub for zinc smelting for a numbers of reasons, which include the following; lower pollution and safety standards, proximity to end use manufacturing facilities and, finally, has a population which is increasingly headed towards urbanization, creating huge demand for zinc construction materials.
On a global scale, smelter capacity is forecasted to increase slightly to around 16 million t/y over the next 5 years from its current 2016 base of around 15 million t/y. Over the next 5 years, China is showing the most promise for expansion in smelting capacity as the rest of the world appears set to only replace the capacity that they are scheduled to lose over the same period.
Smelter Closures are led by Padeng’s Tak smelter, located in Thailand, which is set to close once the nearby Mae Mod Mine is depleted of its ore. This will remove 110,000 t/y capacity from the smelting market. Also, closer to home, the zinc recycler, Horsehead, headquartered in Pittsburgh, Pennsylvania, is just emerging from Chapter 11 Bankruptcy , eliminating its outstanding debt with a new deal. That said, their Mooresboro smelter has a lot of technical issues to work through before it can be restarted, so until that happens, it must be considered lost capacity.
The loss in capacity will be filled with some expansion of existing smelting operations. A couple of the larger planned expansions are: Penoles’ Torreon smelting operation, which is set to expand its operation somewhere in the order of 100K t/y over the next 5 years. Also, but on a smaller scale, Boliden’s Odda and Vendanta’s Skorpion look to expand their capacity in the next 5 years.
In all, much like zinc mine production that’s outside of China, the impact of the new smelting capacity will be mostly nullified by the amount of smelter closures or production reductions. If there is to be growth in smelting capacity, it will come from China.
NOTE: I’ve found it difficult to find and confirm information on the Chinese zinc supply and demand fundamentals from sources that I trust.
Zinc Uses
Zinc is a metal which plays a significant yet inconspicuous role in our everyday lives. Its most desirable attribute is the fact that it’s resistant to corrosion. Through the galvanizing process, industries have leveraged this attribute to improve the quality of their products and, thus, deliver tremendous value to their customers.
Most of us commute to work in a mode of transportation that likely has a galvanized body. Or, we live in a home with a galvanized steel roof or building exterior.
Source: Zinc: Essential for Modern Life – International Zinc Association ~ pg.12
Other than its corrosion resistance, zinc is also in demand for its calenderability, abrasive resistance, cast-ability, and room temperature mechanical properties. Each of these properties have a different application within industry.
Galvanizing
Zinc’s most common use is in the galvanizing of steel. While the zinc barrier created in the galvanizing process creates a barrier between moisture and the underlying steel, the zinc does itself break down in the presence of moisture, albeit at a much slower rate than steel. Thus, the thickness of the zinc coating will dictate the life of the corrosion protection.
The International Zinc Association provides the following example of the effectiveness of galvanized steel within the automotive industry,
“The use of galvanized sheet for automotive body panels allows today’s automakers to guarantee up to 12 years’ corrosion resistance, while adding only a fraction of a percent to the cost of the vehicle. The cost-benefit ratio represents outstanding value for the consumer.” ~ IZA
- While the galvanizing of rebar for construction purposes exists today, it may get a huge boost in the near future as a few of the southern States in America look to increase the grade of rebar used within all of their marine construction. For those who don’t know, my background is in steel manufacturing. I was General Foreman of operations at a rolling mill which produced rebar, angles, channels and flats.
- Typically concrete / rebar construction is designed with 25 to 50 years life span, however, marine construction, in particular, has come under scrutiny for not being robust enough, which has prompted some States to look at increasing their construction specifications on the materials used in marine construction. For rebar, this means higher grade requirements and possibly being restricted to only corrosion resistant steel.
- Currently, epoxy coated rebar is used for applications that require corrosion resistance, however, epoxy coating has been known to crack, allowing for moisture to begin its oxidation of the steel.
- Stainless rebar is an option, as high nickel/chromium levels provide the steel with corrosion resistance, but require specialized rolling mill layouts to accommodate its production. If stainless rebar were to be mandated, eventually some efficiency would be made to reduce its higher production costs.
- Galvanized rebar is a very promising prospect as a galvanizing line could be added to the end of most rebar mills without a major cost in CAPEX or in process changes, unlike stainless. The knock on galvanizing is that it’s only a surface coat, which does corrode over time. That said, an appropriate zinc coating could meet the 100 year life span requirements.
For the reasons outlined, galvanized rebar could play a major role in marine construction’s future and further drive zinc demand.
Sheet or Rolled Zinc
- Zinc is melted and continually cast into ingots. Present day casting equipment will deliver an ingot in the near net shape of the final product, thus drastically reducing the amount of time and the number of rolls needed to reduce the ingot into its final finished product dimensions.
- Zinc’s chemical and mechanical properties make it a go to metal within the construction industry. Specifically, using it in applications which take advantage of its corrosion resistance, such as roofs or exterior wall material.
- A roof or building wall constructed using the sheet or rolled zinc has a typical life span of upwards 100 years. This life span provides the customer with superior bang for their buck, and because approximately 90% of the material is recycled, it reduces the amount of waste sent to landfills.
- I believe corrosion resistant building materials, such as those which use zinc, will be in growing demand in the future.
Die Casting
Zinc’s mechanical properties make it ideal for die casting. Its strength and stiffness allow for thin-walled sections to be cast, reducing the casting time, the amount of zinc needed to produce the product, a reduction in tooling costs, and allows for a less complex assembly of the product being manufactured.
Brass
Brass is a combination of zinc and copper which, depending on the concentration of each metal, can have very different properties. Most commonly, brass is strong, machineable, tough, conductive and corrosion resistant. Brass’ uses range from pump parts to clock components, bushing material, and a variety of marine applications. The variety and number of uses explains why brass makes up 9% of zinc’s demand.
Zinc Dust
Zinc dust is a fine gray powder, which can be used within paints to leverage zinc corrosion resistance. It can be a cheaper option than buying galvanized steel, but isn’t as effective as the galvanized product.
Fertilizers
While currently accounting for only a small portion of zinc’s uses, zinc fertilizer is on the rise, as organizations like the Zinc Nutrient Initiative produce research on the positive effects that zinc fertilizers have on crop yields around the world. By increasing a plant’s water uptake ability, zinc improves the plant’s resilience to drought and pathogenic infections and, thus, increases crop yields.
Demand for Uses
A growing trend in the world is the urbanization of the population which, in countries like China, is happening at a rapid pace. The urbanization of the population leads to a whole host of demands, but most importantly in context to my commentary on zinc, is building materials. Whether it be for city infrastructure or for residential building projects, corrosion resistant materials use is on the rise, as more and more homeowners seek to extend the lives of their homes and vehicles.
Zinc Alternative
At some point in the future, the zinc price will either force manufacturers to find an alternative material, or economics will allow manufacturers to use a superior substitute.
One building material substitute could be stainless steel; its corrosion resistance is not a coating but found throughout the metal, and it’s strong, both of which make it ideal for use with infrastructure that requires longevity. For roofing material, stainless has a higher melting temperature leaving it less susceptible to damage in house fires. Also, it’s more dent-resistant and will not deform under foot or in a hail storm which, depending on the climate in which you live, could be advantageous.
Aluminum and magnesium alloys could replace zinc in casting, as they have some similarities in mechanical properties, but it really depends on the end use as to whether the zinc can be replaced economically. In some cases, plastics may even be used to replace zinc.
Fertilizer is a very small part of zinc demand, but in a situation where the price is elevated, my guess is that farmers simply won’t use it. In a world with a “warming climate,” droughts may become all too common and, therefore, we may see more farmers changing their view of the use of zinc-rich fertilizers.
A quick glance at a few replacement metal prices: Stainless steel – depending on the grade and how it’s manufactured, the price can range between USD $2000 to $3000 per tonne; Aluminum – LME cash price USD $1937 per tonne; Molybdenum – LME cash price USD $14,750 per tonne; and finally, plastics — there can be a wide range of prices depending on chemistry.
Supply and Demand Comparison
Source: International Lead and Zinc Study Group
As you can see in the graph, demand out-paced both the refined metal and mine production in 2016 by 286K and 724K, respectively. From the supply side, 2017 is looking much like 2016, except the deficit between demand and supply appears as though it could get even worse as the mine closures and production losses add up in the immediate future. The main wildcard on the supply side commentary is Glencore’s 500K of missing capacity, which could come back online at any point, but like Nyrstar’s Middle Tennessee operations, will most likely take 6 to 12 months to hit full production.
Nevertheless, in the zinc market’s current state, I think we’re in for higher prices at least until some point in 2018, when Glencore and some new production capacity can possibly send some doubt or correction into the zinc price. In the meantime, could the $3000 per tonne level be achieved? I don’t see why not.
Source: International Lead and Zinc Study Group
Zinc’s bullish narrative is based on falling supply; prices must rise to bring on more production and to force end use manufacturers into using other metals for their products and, thus, erode the currently steady zinc demand profile.
In the weeks ahead, I’m going to take a closer look at the zinc exploration and development companies, which I believe are in a great position to provide us with good speculative value during this zinc bull market.
Don’t want to miss a new investment idea, interview or financial product review, become a Junior Stock Review VIP now – for FREE!
Until next time,
Brian Leni P.Eng
Founder – Junior Stock Review
Sources:
Australian Atlas of Minerals Resources, Mines & Processing Centres
International Zinc Association
Disclaimer: This is not an investment recommendation, it is an investment idea. I am not an investment professional, nor do I know you and your specific investment criteria. Please due your own due diligence. I have NOT been compensated to write this article and do NOT have a business relationship with any of the companies mentioned in this report. I do NOT own shares in any company mentioned.